What are AGVs and AMRs? A deep analysis of automation progress in logistic facilities and next generation autonomous (collaborative) mobile robots!
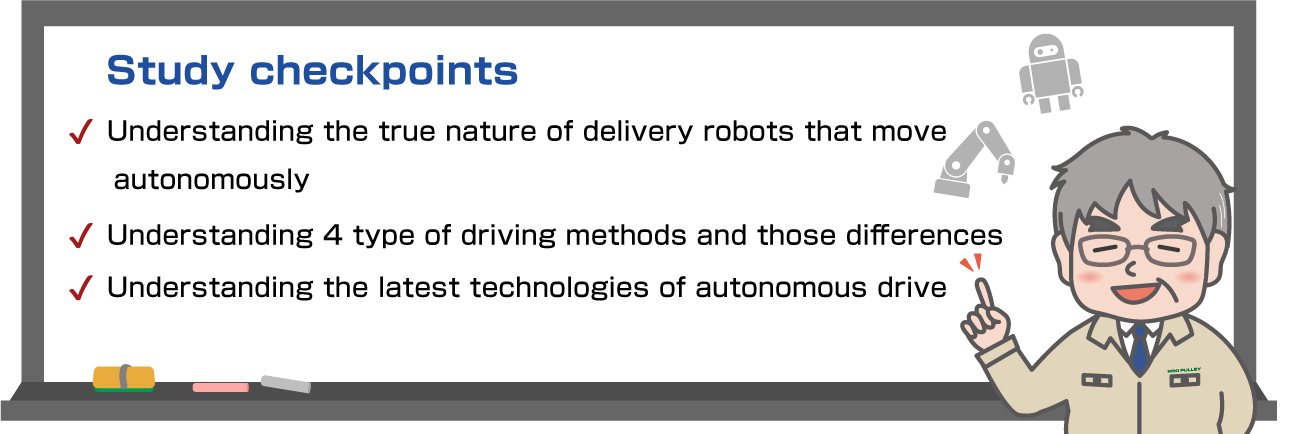
Are there really autonomous mobile robots?
What is an AGV (automated guided vehicle)?
Ms. Hama: Mr. Hashimoto! The other day, I found an automated guided vehicle operating in the factory! I’ve heard that they can transport many different kinds of large quantity goods inside the warehouse without an operator!
Mr. Hashimoto: That’s right. They are called AGVs (automated guided vehicles). Using guidance methods such as strips of magnetic tape, AGVs can take the place of human workers by carrying required components to the required place without interrupting the work flow. As well as operating in factories and warehouses, AGVs are also used for deliveries, security and cleaning in smart buildings.
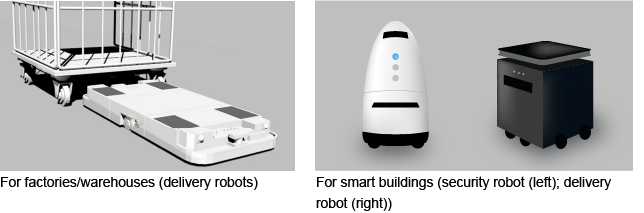
What is an AGV (automated guided vehicle)?
This is an acronym for Automated Guided Vehicle. In JIS D6801 standard, they are described as: “Vehicles that have functions of transporting non-human items such as freight. Run automatically in a certain area, not allowed to run on roads designated in the "Road Traffic Law". AGV run along routes determined by guidance methods using magnets, lasers or optical signal.
Types of driving methods for AGVs
Guidance method | Features | images | |
---|---|---|---|
First Generation | Electromagnetic guidance | An extremely weak AC current flows along metal strips set on the floor, AGVs move along the strips by using sensors to detect the magnetic field | ![]() |
Magnetic guidance | Magnetic rods or tape are set on the floor and AGVs are guided by magnetic sensors. This is the most widely used method in Japan. And it is likely the systems will transition to 2nd-generation, 4th-generation or hybrid models in near future. | ||
Second generation | Image recognition | AGVs determine their locations by scanning symbols such as QR codes or AR markers on the floor or ceiling. This system enable high precise positioning. | ![]() |
Third generation | Laser (reflectors) | Reflectors are attached on walls and pillars in the building. AGVs estimate their own locations by using reflected laser beams and run autonomously. Sufficient reflectors must be installed throughout the area for vehicle operation. | ![]() |
Fourth generation | SLAM Self position estimation and mapping (SLAM) ・Visual SLAM ・LiDAR SLAM |
Vehicles driven by self position estimation function. It is by sensors such as cameras and lasers coupled with encoders or gyroscopes. The vehicles can drive autonomously, no need to install a guidance system. These are often called as autonomous (collaborative) mobile robots (AMRs), unguided AGVs or next-generation AGVs. | ![]() |
• While the term AGV has been widely adopted around the world, autonomous versions are now often called AMRs to distinguish them from non-autonomous vehicles.
Mr. Hashimoto: AGVs have been used for long time and can drive automatically with high precision. But they couldn’t determine their own route or drive avoiding obstacles on their way.
What is an AMR (autonomous (collaborative) mobile robot)?
Ms. Hama: Aren’t there any robots that can determine their own routes as they drive?
Mr. Hashimoto: Robots that can move around autonomously are called autonomous (collaborative) mobile robots (AMRs). Some people also call them unguided AGVs or next-generation AGVs.
■What is an AMR (Autonomous (collaborative) Mobile Robot)?
This is an acronym for Autonomous (collaborative) Mobile Robot. These robots don’t need a guidance system and use built-in LiDAR to estimate the distance to walls and pillars. They build up a map of the surrounding environment and use systems to estimate their own position on that map. In JIS D6802 “Automatic guided vehicle systems−General rules on safety”, they are described as “automated transportation systems that transport and handle goods using automated guided vehicles that co-exist with human and shared by human in their operating area.”
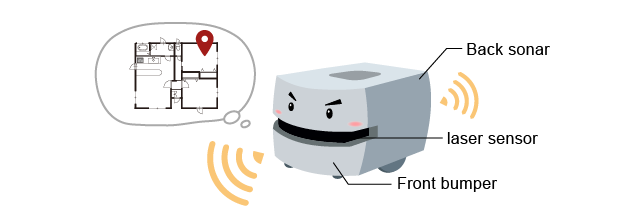
Ms. Hama: Now there are AMRs (autonomous (collaborative) mobile robots) that can driven by themselves. So products and components can be collected and transported automatically.
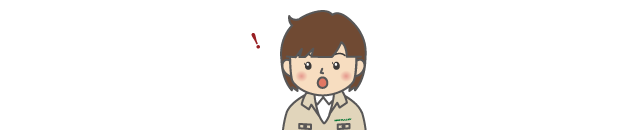
How does an AMR (autonomous (collaborative) mobile robot) differ from an AGV (automated guided vehicle)?
Ms. Hama: The products and components that they can carry are the same, aren’t they? So, what exactly are the differences between an AMR (autonomous (collaborative) mobile robot) and an AGV (automated guided vehicle)?
Mr. Hashimoto: Basically, AGVs (automated guided vehicles) are like trains running on fixed rails. On the other hand, AMRs (autonomous (collaborative) mobile robots) are more like cars running in collaboration with people. If we focus on the guidance method, you can see the differences shown in the table . Some hybrid models have also been released recently. And AMRs (autonomous (collaborative) mobile robots) are sometimes used together with cobots.
The difference between an AMR and an AGV
AGV | AMR | ||
---|---|---|---|
Electromagnetic guidance | Image recognition | SLAM | |
Magnetic guidance | Laser guidance | ||
Precisions | ○ | △ | △ |
Flexibility | ✖ | △ | ○ |
Simplicity | ✖ | ○ | ○ |
Reliability | ○ | △ | △ |
Cost | ○ | △ | △ |
Ms. Hama: So, the cobots we learned before are also used here, right?
* See here for details ▶ Cobot? Introduction to how safety is assured for robots, machines and people
What are the key elements in AMRs (autonomous (collaborative) mobile robots) and AGVs (automated guided vehicles)?
Ms. Hama: Could you tell me what are the key elements of AMR (autonomous (collaborative) mobile robot) and AGV (automated guided vehicle)?
Laser SLAM technology to detect obstacles
Mr. Hashimoto: Fourth-generation AMRs (autonomous (collaborative) mobile robots) generally use a SLAM system. They use cameras and laser sensors to observe their surroundings and estimate their own position by both encoders or gyroscopes. Products related with SLAM technology include the latest models of cleaning robots, deliveries by automatically controlled drones and even the Mars exploration rover.
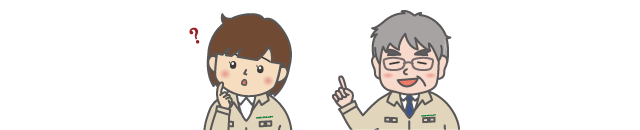
■What is SLAM technology?
Here we refer to SLAM (simultaneous localization and mapping) technology. SLAM enables a vehicle to estimate its own position (localization) and create a map of sorouding environment (mapping).
Ms. Hama: So, SLAM technology is also used in our familiar places!
Visual SLAM and LiDAR SLAM
Mr. Hashimoto: There are 2 types of SLAM technology. One is called visual SLAM based on images captured by cameras, the other called LiDAR SLAM, based on point cloud data measured by LiDAR.
■Visual SLAM
This technology uses captured images by single or double-lens cameras to estimate sorrounding area map , 3D information and it's own position at the same time.
■LiDAR SLAM
Laser sensors (distance sensors) so called LiDAR (light detection and ranging) generate point cloud data of surrounding area. Then create 2D map of surrounding area in real time and localizing own posision on the map at the same time.
Mr. Hashimoto: LiDAR is used in self-driving cars, drones and even in the iPad Pro released in March 2020. Now there are new apps that make it easy to create augmented reality (AR) models by scanning a 3D space.
Ms. Hama: I recently used an augmented reality (AR) app that let me try out furnitures at home! We can feel further technology evolution!
Emergency stop function
Mr. Hashimoto: Recently, AMRs (autonomous mobile robots) and AGVs (automated guided vehicles) has been developed in various sizes, from small up to very large. In the case of large products or components, they can carry loads of 1 ton or even more.
Ms. Hama: That’s amazing! May be the function needed in emergent case will increase!
Mr. Hashimoto: That’s right. Typical one is spring-actuated brakes. There are various requirements of an emergency stop brake for AMRs and AGVs that move around night and day.
• The brake must be capable enough to stop heavy loads
• The brake must be highly reliable
• The brake must have long (service) life
• The brake must be very easy to maintain
• The brake must be power consumption saving
(for battery-driven AMRs (autonomous (collaborative) mobile robots) and AGVs (automated guided vehicles)
■AGV drive wheel
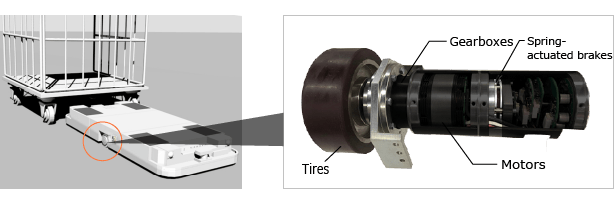
Mr. Hashimoto: This photo shows the structure of AGV drive wheel with built-in motor. The item in the middle part is a spring-actuated brake. In case of independent motor type, it is best to use coupling to connect wheel with motor. This makes it easy to remove and improves work efficiency during maintenance.
■ Example of coupling installation
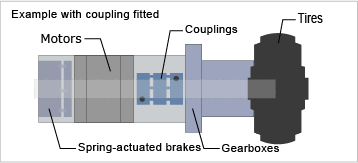
Ms. Hama: So, it is really important for safty operation of AMR (autonomous (collaborative) mobile robot) or AGV (automated guided vehicle) to install spring-actuated brake and coupling.
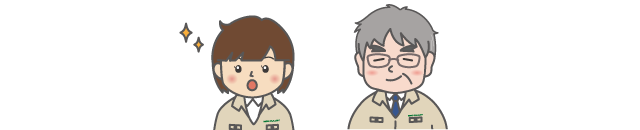
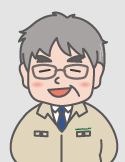
Mr. Hashimoto, Miki Pulley Co., Ltd
Joined Miki Pulley in 1972. Worked as a Product Manager in the Marketing and Technology divisions in positions both in Japan and overseas. He has also been involved with other organizations through joint research projects with universities and specialist bodies. He currently works as technical adviser and staff trainer.
